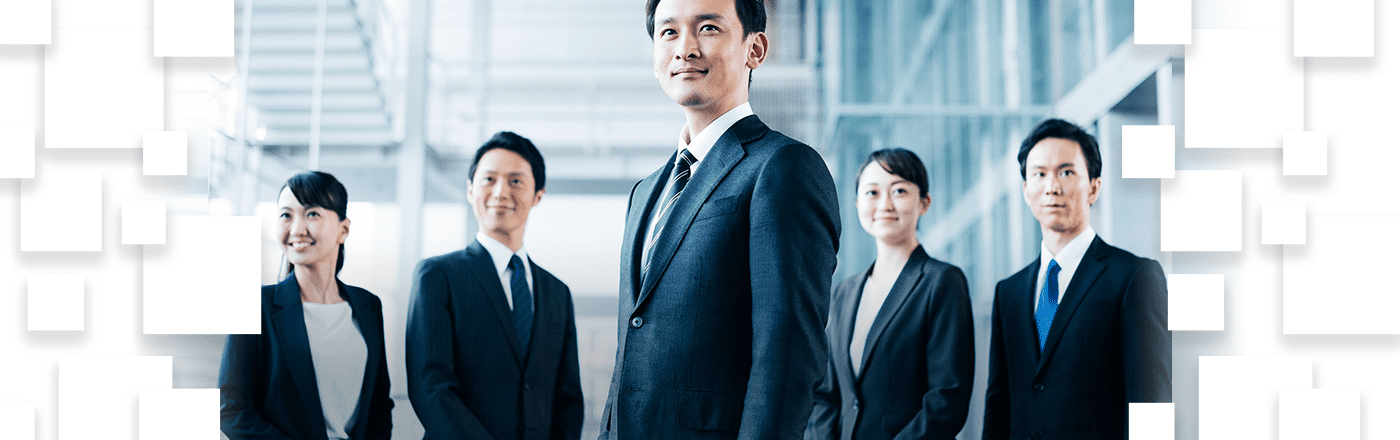
本当に何も知らないけど、なんか難しそうだなぁ・・・
TPS改善って「乾いた雑巾を絞る」というイメージが強く、職場の雰囲気がピリピリして悪くなるのではないか心配・・・
熟練の手わざ作業ばかりで、変化に根強い抵抗感もあり改善は無理だろうな・・・・
以前、改善指導グループが当社に入ったときはトップダウン指示でやらされ感だけが強く残っている。これも同様のイメージ?
ご心配はいりません!
大手部品製造会社の人材育成部門にて新入社員から現場管理監督者まで、更には海外若年技術者、仕入先改善指導育成など長年に渡り実践指導してきました。その豊富な知識と経験を活かし「貴社のお悩みに寄り添いながら共に成長する」育成コンサルティングを進めていきます。
生産性向上等の改善支援には、多くのコンサルタントを有した有名コンサル会社が日本には数多くあります。しかしそうした会社への依頼では従業員数が100人を超える比較的大きな事業規模の企業が対象で、また実力ある有力コンサルと合わせて自前スタッフが組織的かつ強力に推進していくものが多いものです。
それに対して当社のような独立系コンサルは、従業員数20人弱の中小企業を主な対象とし、代表の大脇が直接指導を行いながらサポートしていきます。生産性向上はその結果として成るものであくまで育成対象者の成長が目的です。
知識はあってもそれを実践できるか?現場改善というのは実践学であり、理解していても実践できるかどうかは別にあります。「先ずはやってみる」ことが大切です。理解と実践は車の両輪であり、同時に回転することでより多くの学びがあり知識が深まり自己スキルが向上できるのです。しかし、すぐに実践したいができないこともいままでの経験から数多く見受けられました。そこで当社では貴社の環境を踏まえながら育成プランを立て段階的に改善スキルを向上させていきます。
トヨタ生産方式を支える2本柱には、J.I.T(ジャスト・イン・タイム)と自働化(じどうか)があります。その1本の柱である自働化において重要なのは、設備自ら異常に気付き、知らせ、停止し、ロスなくキチンと働く(不良を作らない、流さない)ことが基本です。これが出来ていないと設備効率は大きく下がり生産コストが増大します。
そのためには設備を日常管理しているオペレーターの役割も大変重要になってきます。そこで当社ではTPS改善と並行しながら設備改善指導を通じて可動率向上も必要に応じてサポートできます。その結果、設備を主体とした生産性を大きく向上することができます。